T-shirts have become a canvas for personal expression and powerful branding tools for businesses. Whether you are a budding entrepreneur looking to create a compelling merchandise line or an individual seeking to design a standout custom tee, the quality of t-shirt printing plays a pivotal role in achieving professional-looking results.
In this blog post, we will delve into the intricacies of t-shirt printing, exploring various techniques, design elements, and essential tools required to produce high-quality prints that resonate with your audience.
When it comes to t-shirt manufacturers, the significance of professionalism cannot be understated. For businesses, a well-printed t-shirt can make a lasting impression on customers, fostering brand loyalty and word-of-mouth promotion. A poorly printed t-shirt, on the other hand, can tarnish a brand’s image and lead to customer dissatisfaction.
Similarly, individuals seeking custom tees desire prints that look sharp and vibrant, reflecting their unique style.
Hence, understanding the art of t-shirt print is crucial for ensuring customer satisfaction and establishing a strong brand identity.
Understanding T-Shirt Printing Techniques
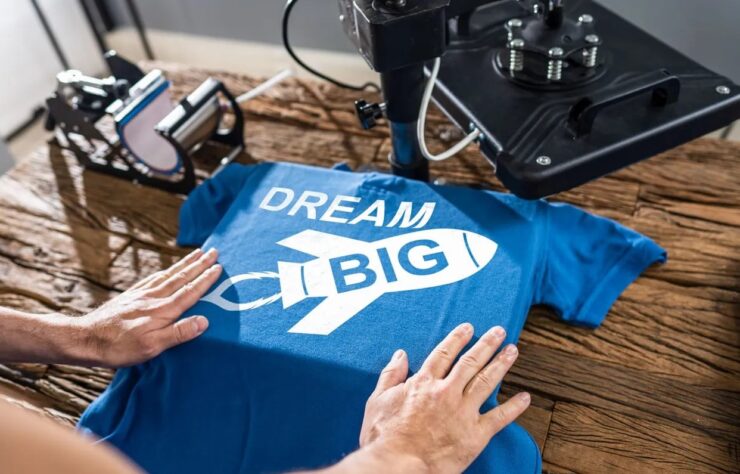
T-shirt printing encompasses a range of techniques, each with its strengths and weaknesses. Screen technique, a traditional method, is ideal for large-scale production and offers unmatched durability but can be costly for smaller batches.
Heat transfer and sublimation printing are suitable for intricate designs and vibrant colors but may lack longevity.
Direct-to-garment (DTG) form allows for photo-realistic prints and is versatile but requires high-quality artwork and specific fabric types. Understanding the strengths and limitations of each technique enables you to make informed decisions based on your printing requirements.
Choosing the Right T-Shirt and Fabric
Selecting the right t-shirt and fabric is pivotal for achieving outstanding print results. Cotton is the most common fabric choice due to its affordability and versatility, but blends like polyester-cotton offer enhanced printing options.
Tri-blends provide a luxurious feel but may require specialized techniques. Additionally, the weight and thread count of the fabric play a significant role in how ink adheres to the material.
Matching the t-shirt type to the printing technique and design complexity ensures optimal results that align with customer preferences. Also, you need to select the right manufacturer, and t shirt printing UK could be your answer in this domain.
Creating an Eye-Catching Design
An eye-catching design is the heart of any successful t-shirt creation endeavor. Understanding your target audience and tailoring designs to resonate with their preferences is essential.
Color choices evoke emotions and must align with the message or brand identity, while typography and layout dictate the overall aesthetic. Achieving balance in design elements ensures that the message is conveyed effectively and appeals to a diverse audience.
Preparing Artwork
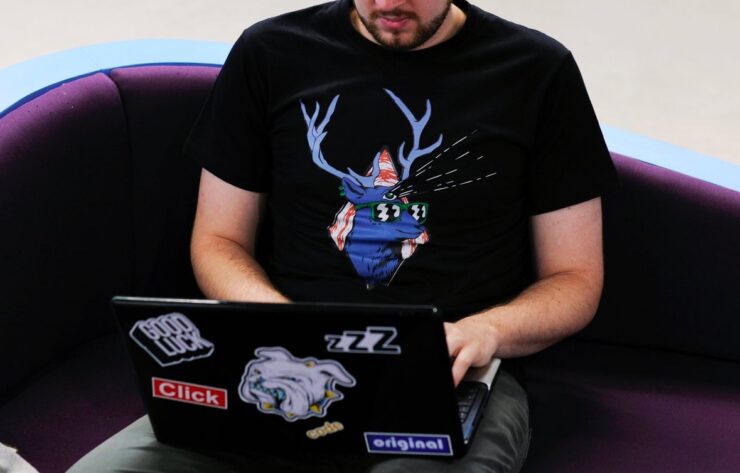
To ensure professional-looking prints, high-resolution artwork is paramount. Low-quality images can result in pixelation and blurry prints, diminishing the impact of the design. Providing artwork in vector formats ensures scalability without loss of quality.
Additionally, understanding the color spaces used in printing and converting artwork to the appropriate color profile is crucial for achieving accurate color representation.
Screen Printing: Step-by-Step Guide
Screen printing is a revered technique known for its durability and versatility. The process involves creating a stencil on a mesh screen, which allows ink to pass through onto the t-shirt. Selecting the right mesh count, preparing screens with precision, and ensuring accurate registration are vital for achieving consistent and professional prints.
Heat Transfer and Sublimation Printing: Best Practices
Heat transfer and sublimation printing are popular choices for intricate designs and full-color prints. Heat transfer involves applying pre-printed designs using heat and pressure, while sublimation transfers ink to the fabric through a heat-sensitive dye.
Adhering to best practices, such as using high-quality transfer paper and maintaining precise heat and pressure levels, ensures vibrant and long-lasting prints.
Direct-to-Garment (DTG) Printing: A Comprehensive Guide
DTG printing is a cutting-edge technology that allows for detailed and photo-realistic prints. Pre-treatment of the fabric and curing of the ink are crucial steps to ensure optimal adhesion and color vibrancy.
Additionally, post-printing care, such as proper washing and drying, helps preserve the quality of DTG prints.
Equipment and Tools for T-Shirt Printing
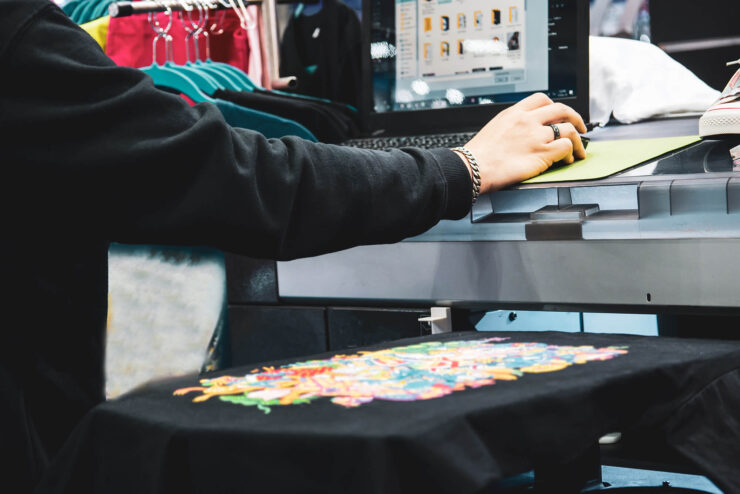
Equipping yourself with the right tools is essential for successful t-shirt printing. For screen printing, you’ll need screens, squeegees, and exposure units. Heat transfer requires heat presses and quality transfer paper.
Sublimation printing necessitates a sublimation printer and heat press. DTG printing involves investing in a DTG printer and pretreatment machine. Understanding budget-friendly options and advanced machinery allows you to make informed decisions based on your printing needs and budget constraints.
Testing and Quality Control
Before embarking on full-scale production, testing prints are imperative. Testing allows you to identify and rectify issues, ensuring consistency in print results. Conducting color tests, verifying design alignment, and assessing ink adhesion enable you to deliver flawless prints to customers.
Caring for Printed T-Shirts
Educating customers on how to care for printed t-shirts is vital for maintaining print quality and longevity. Proper washing and drying instructions, along with tips for ironing and pressing, ensure that customers can enjoy their custom tees for years to come.
Troubleshooting Common Printing Issues
Despite meticulous preparation, t-shirt printing may encounter challenges. Identifying common issues like color bleeding, ink curing problems, and misprints empowers you to troubleshoot effectively. Addressing these issues promptly and efficiently minimizes waste and ensures customer satisfaction.
Conclusion

Mastering the art of custom t-shirt printing is a journey that involves understanding various printing techniques, selecting the right materials, designing eye-catching artwork, and using the appropriate equipment.
Armed with these valuable insights and best practices, you can achieve professional-looking prints that resonate with your audience, whether you are a business owner seeking brand promotion or an individual expressing your creativity.
By dedicating time and effort to hone your t-shirt creation skills, you can elevate your prints from ordinary to extraordinary, leaving a lasting impression on everyone who wears your creations.
So, seize the opportunity to apply the tips and techniques discussed in this blog post, and let your t-shirt printing endeavors shine with unmatched professionalism and creativity.